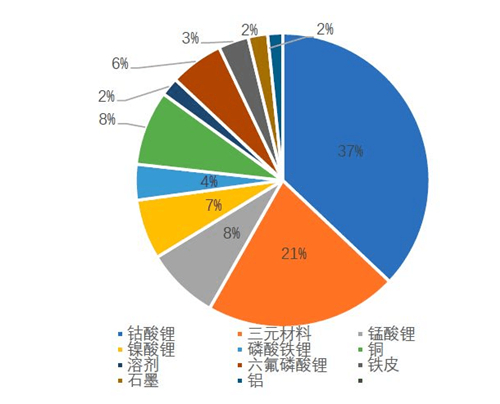
基于鋰電池正負極結構及其組成材料銅、鋁與正負極材料的物料特性,采用錘振破碎、振動篩分與氣流分選組合工藝對廢鋰電池正負極組成材料進行分離與回收。實驗采用ICP-AES分析實驗樣品與分離富集產品的金屬品位。結果表明:該正負極材料經破碎篩分后,粒徑大于0.250 mm的破碎料中銅、鋁的品位為92.4%,而粒徑小于0.125 mm的破碎料中正負極材料的品位為96.6%,均可直接回收;粒度為0.125~0.250 mm的破碎料中,銅、鋁的品位較低,可通過氣流分選實現銅、鋁與正負極材料的有效分離回收;氣流分選過程中,操作氣流速度為1.00 m/s時,銅、鋁的回收率達92.3%,品位達84.4%。
1)通過錘振破碎、振動篩分與氣流分選組合工藝可實現對廢鋰電池正負極材料中金屬銅、鋁與正負極材料的資源化利用。
2)正負極材料經過錘振破碎可有效實現碳粉與銅箔、鋁箔間的相互剝離,后經基于顆粒間尺寸差和形狀差的振動過篩可使銅箔、鋁箔與正負極材料得以初步分離。錘振剝離與篩分分離結果顯示,銅、鋁與正負極材料分別富集于粒徑大于0.250 mm和粒徑小于0.125 mm的粒級范圍內,品位分別高達92.4%和96.6%,可直接送下游企業回收利用。
3)對于粒徑為0.125~0.250 mm且銅、鋁品位較低的破碎顆粒,可采用氣流分選實現銅、鋁與正負極材料間的有效分離,當氣流速度為1.00 m/s時即可取得良好的回收效果,金屬銅、鋁的回收率可達92.3%,品位達84.4%
4)該設備主要用于鋰離子電池生產廠家,對報廢正負極片中的正負極材料進行分離處理,以便循環利用之目的。成套設備在負壓狀態中運作,無粉塵外瀉,分離效率可達98%以上。